Check out our new Substack, Merchandise Trade With Legion
Different Types of Refractory Castables and Their Applications
This blog explores the various types of refractory castables, including their composition, properties, and uses across different industries. It provides a comprehensive understanding of how castables enhance industrial performance and withstand extreme conditions.
ENGLISH
3 min read
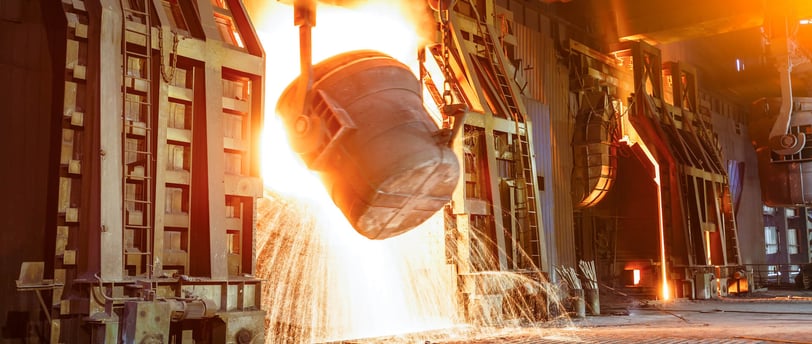
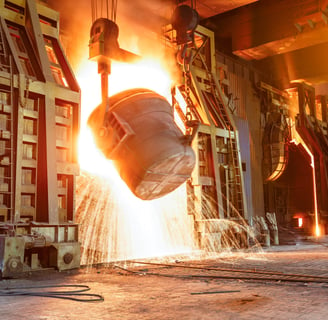
Refractory castables are a type of monolithic refractory material used to line furnaces, kilns, and other high-temperature equipment. They are supplied as dry mixes that are combined with water before installation, allowing them to be cast or molded into desired shapes. Unlike bricks, castables offer the flexibility of creating seamless linings and repairing existing structures without the need for joints.
These castables are designed to endure harsh environments involving high heat, mechanical stress, and chemical corrosion. Their use extends across industries such as steel, cement, petrochemical, and power generation, where durability and performance are critical to operational efficiency.
Classification Based on Binder Material
The binder in a refractory castable plays a key role in determining its properties and performance. Below are the major types:
Calcium Aluminate Cement (CAC) Castables
Composition: Made with calcium aluminate cement as the binder, along with refractory aggregates.
Properties: Fast setting, high early strength, and resistance to chemical corrosion.
Applications: Widely used in steel and cement industries for ladles, preheaters, and rotary kilns.
Hydraulic Bond Castables
Composition: These castables use hydraulic cement that hardens when mixed with water.
Properties: Quick hardening and good mechanical strength.
Applications: Ideal for applications in boilers and incinerators that require fast installation and drying times.
Classification Based on Installation Method
Different castables require specific installation techniques depending on their flow and workability.
Conventional Castables
Require vibration during installation to achieve proper compaction and bonding.
Properties: Moderate strength with a dense structure.
Applications: Suitable for areas that experience mechanical stress, such as steel furnaces and industrial kilns.
Self-Flow Castables
Can flow freely into molds or lining areas without vibration.
Properties: Easy to install in complex or intricate shapes.
Applications: Cyclone separators, burner blocks, and other equipment with intricate geometries.
Classification Based on Alumina Content
The alumina content in refractory castables directly influences their ability to withstand high temperatures and chemical attacks.
Low-Alumina Castables (Below 50% Alumina)
Properties: Economical, but offer lower resistance to abrasion and wear.
Applications: Suitable for moderate-temperature areas, such as boilers and insulation layers.
High-Alumina Castables (Above 50% Alumina)
Properties: Highly resistant to heat, chemical attack, and mechanical wear.
Applications: Used in blast furnaces, rotary kilns, and other high-temperature environments.
Insulating vs. Dense Castables
Depending on the need for heat conservation or durability, castables can be classified into insulating and dense types.
Insulating Castables
Composition: Contain lightweight aggregates like perlite or vermiculite.
Properties: Low thermal conductivity, minimizing heat loss.
Applications: Lining of furnaces to improve energy efficiency and reduce fuel consumption.
Dense Castables
Composition: Made with heavier aggregates for increased strength.
Properties: High mechanical strength and resistance to abrasion.
Applications: Used in high-wear areas such as burner blocks and impact zones in cement plants.
Special Castables for Corrosive Environments
Certain environments expose refractory linings to harsh chemicals, requiring specially formulated castables.
Acid-Resistant Castables
Composition: Made with silica-based materials.
Properties: Excellent resistance to acidic fumes and chemical attacks.
Applications: Chimneys, ducts, and flue gas systems in chemical plants.
Alkali-Resistant Castables
Composition: Typically contain high alumina content to withstand alkali attack.
Properties: Prevent deterioration from alkali vapors.
Applications: Cement kilns, boilers, and incinerators.
Key Properties and Performance Indicators
Thermal Shock Resistance: Ability to withstand sudden temperature changes without cracking.
Mechanical Strength: High compressive strength to resist heavy loads and abrasion.
Chemical Resistance: Protects against corrosion from molten slag, gases, and alkalis.
These properties make refractory castables ideal for use in critical industrial processes that require durability and consistent performance under harsh conditions.
Industrial Applications Across Different Sectors
Refractory castables play a crucial role in several industries:
Iron and Steel Industry: Lining for blast furnaces, ladles, and tundishes to handle molten metal.
Cement Industry: Used in rotary kilns, preheater towers, and clinker coolers to resist high temperatures.
Petrochemical Industry: Lining for cracker units, reformers, and heat exchangers.
Power Generation: Boilers, incinerators, and waste-to-energy plants benefit from castables due to their thermal insulation and durability.
Advantages of Using Refractory Castables
Cost-Effective Repairs: Castables can be easily applied to repair worn-out linings without dismantling equipment.
Energy Efficiency: Insulating castables reduce heat loss and improve operational efficiency.
Versatility: Available for various industrial needs, from lightweight insulation to heavy-duty abrasion resistance.
Seamless Installation: Can be molded into complex shapes, ensuring seamless linings without joints that could weaken over time.
Conclusion: Choosing the Right Refractory Castable
Selecting the right type of refractory castable depends on the specific requirements of your application. For high-temperature environments, high-alumina castables offer excellent resistance, while insulating castables improve energy efficiency by minimizing heat loss. The choice between conventional and self-flow castables depends on the installation environment and geometry of the equipment.
With the right refractory solution, industries can enhance productivity, reduce downtime, and extend the lifespan of their equipment. Whether in steel manufacturing, cement production, or power generation, the correct application of refractory castables is essential for ensuring safe, efficient, and sustainable operations.